
Cognex In-Sight 2000 camera scanning a chain link.
Chain drives are a critical part of the manufacturing process in many industries, whether the chains act as conveyors for glass containers or transport automotive frames down kilometer-long production lines. Regardless of the industry, the vibration and constant pull on chain links can stretch, distort, and even break weakened links if they are not properly maintained, causing unplanned downtime as well as lost productivity and profits.
The automotive manufacturing industry’s traditional dependence on chain drives has prompted production engineers to look for better ways to monitor chain drives. Until recently, automotive manufacturers inspected each link using a rectangle of metal of the same length as a new chain link. A technician visually checked each link as it passed. If a link looked problematic, the technician marked the chain and hoped it would continue to function until the next scheduled maintenance. If the chain broke in the meantime, the manufacturer incurred expensive downtime until the chain could be repaired.
Working with Cognex, engineers at automotive manufacturer General Motors of Canada Company (GM Canada) developed a chain drive stretching system that measures every link in real time and automatically marks non-compliant links without slowing or stopping the line. After discarding a solution that used discrete photoelectric sensors combined with laser pointers to measure chain link lengths, GM Canada engineers developed a real-time chain link monitoring system based on a Cognex In-Sight 2000 vision sensor.
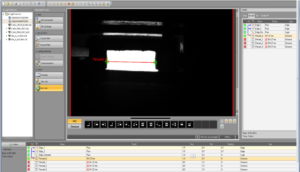
In-Sight software in“easy builder view” for chain-stretch monitoring. The center image shows a chain link and its internal length. The top right column shows the In-Sight Explorer algorithms used in the inspection process, while the lower section shows the pass/fail result for each chain link.
The In-Sight 2000 solution uses a red LED illuminator to backlight the chain to provide a crisp outline of the link under inspection, while a complementary red filter helps eliminate the effects of ambient light.
A proximity sensor provides the trigger signal to the camera as each link passes within its field of view.
Cognex’s In-Sight Explorer image processing software takes the images and runs edge detection algorithms to identify the center of each chain link and then uses a caliper tool to measure the internal length of the chain.
“Basic pass/fail inspections can be accomplished with intuitive, point-and-click setup tools,” says system designer Christopher Eid of GM Canada’s Electrical Engineering–Paint Department. “In this case, edge detection is used to locate the presence of the edges of a link. If both edges are found, the distance between the two connections is measured, and the result is placed under the respective chain-stretch limit category. The result is then sent to the PLC, which then communicates with the HMI and displays the relevant information.”
Using the caliper measurement, GM Canada’s system determines each link’s percentage of variation from the norm. When the variation reaches 4% or more, the vision system sends a signal to a nearby PLC through an optional I/O module. It counts how many chain links fall within each category, as well as the number of rotations for a 1,680-ft chain.

HMI for control and for displaying chain-stretch results.
The PLC allows the user to measure links at the first detection of a conveyor magnet (reference point) by pressing “Start Now” or by discretional scanning. The user can also decide how many revolutions of the conveyor chain the Cognex system will measure during an evaluation session.
“So far, we’ve tested the system on our fastest conveyor,” explains Eid. “We started at 70% coverage because the camera runs faster than the PLC. Today we’re doing most of the analysis on the camera, and we use a 9-frame buffer bit on the Cognex vision sensor, which allows us the ability to cover more coverage per scan. Based on the success of the system, we plan to roll several more systems shortly and eventually modify the system for overhead chains for painting stations too.”
According to Eid, eventually, the PLC will direct a downstream paint sprayer to mark chain links that fall in the 4–5% stretch category for replacement during the next planned maintenance cycle.
As vision sensors gain the speed and power necessary to keep up with the fastest industrial applications, engineers realize that cobbling together discretely wired “dumb” sensors and software is a waste of time and money, especially when vision sensor acquisition and deployment costs are weighed against the regular costs of unplanned downtime.
Cognex
cognex.com
Filed Under: PLCs + PACs