Slip rings excel in myriad designs that include a rotating base or platform — including industrial equipment such as index tables, winders, and automated welders. Wind turbines are another key application — as are medical applications for MRI and CT imaging.
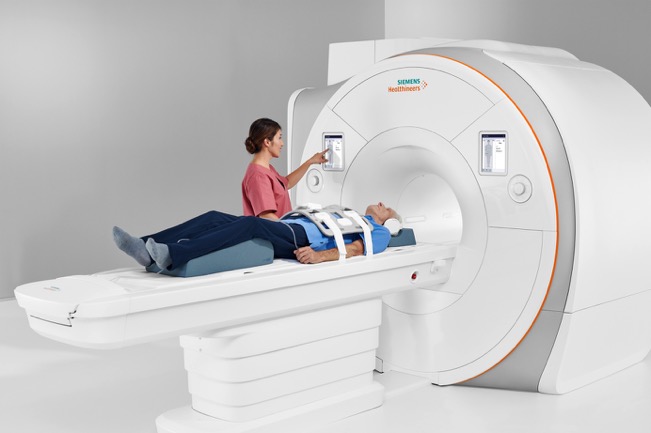
MRI BioMatrix Technology image courtesy Siemens Healthineers
Slip rings also work at the pivot point of closed-circuit security cameras.

Courtesy PowerbyProxi (now of Apple)
Slip rings on amusement-park rides include those that transmit power, control signals, and data to and from the moving sections of carousels, Ferris wheels, and vertical-fall rides. Helicopters, cranes and elevators, generators, and rotating kilns are other examples. Let’s look at a few more in detail.
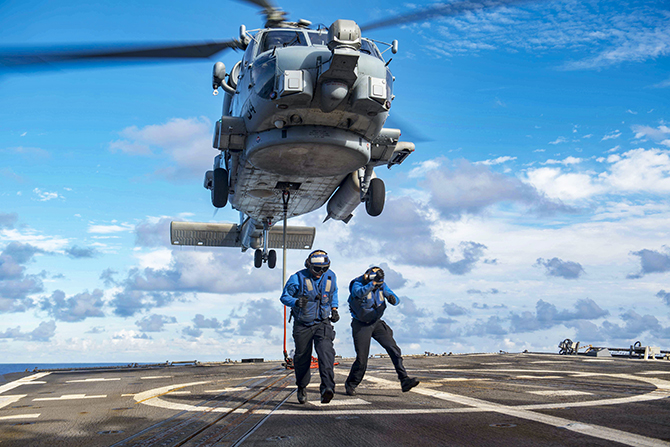
DoD photo: Navy Petty Officer 3rd Class Logan C. Kellums • Navy Petty Officers Melvin Bergado and David Hill-Destefano clear after attaching cargo to an MH-60R Seahawk on the USS Chung-Hoon in the Pacific Ocean.
Slip rings common in wind turbines
Wind-turbine construction on the rise globally, especially in Europe. One challenge is constant exposure to the elements … with only periodic maintenance to clean the turbine of debris and relubricate. That means slip rings must have long-term reliability — with durable contact construction to withstand even peak power output. Offshore turbines especially necessitate highly reliable slip rings due to the cost and time expenditures incurred should they need service.
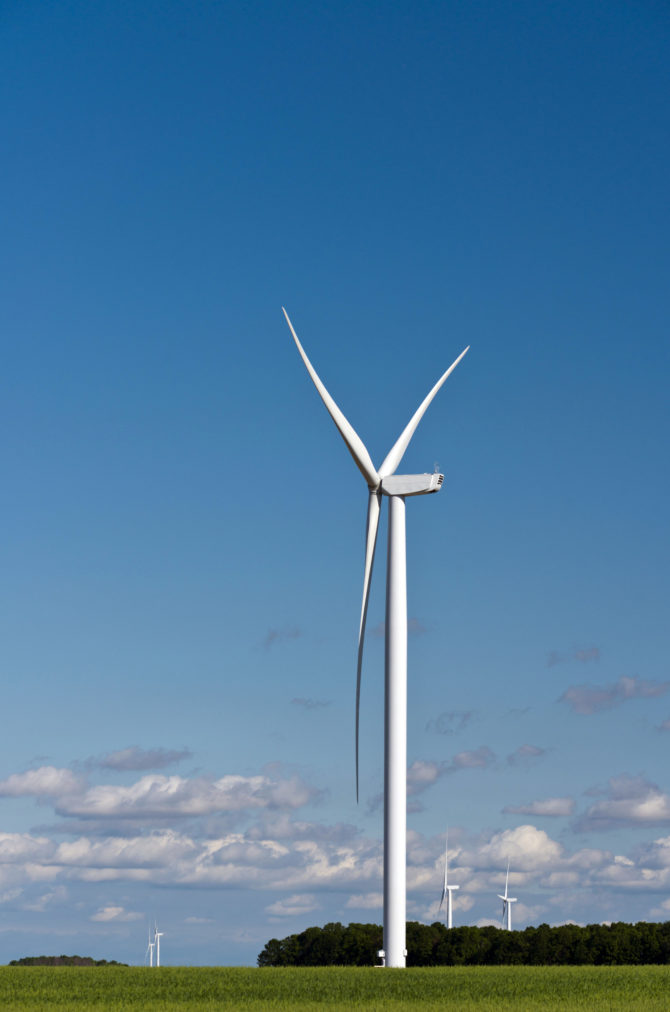
Courtesy Nordex SE
Another challenge is satisfying the requirements of increasingly large and powerful turbines needing exceptional power transfer and transmission of signals for positioning as well as condition monitoring. This includes pitch control with power and commands (via signals over the slip ring) for blade information, hub and pitch motor adjustments, and power backup.
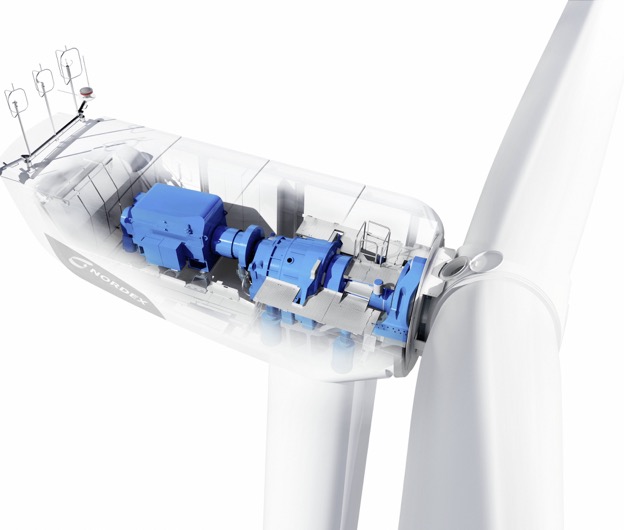
Courtesy Nordex SE
Deublin sells offshore wind-turbine unions that incorporate a slip ring and encoder … with on and offshore assemblies capable of delivering to 250 A — along with Ethernet or EtherCAT or PROFIBUS signals and rotary position tracking — even while rated to IP66 and resisting shock and vibration.
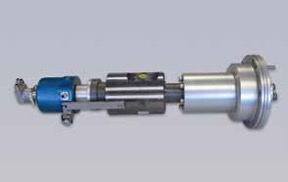
Deublin offshore wind-turbine rotary union
Integrated into a rotary union, these assemblies also accommodate hydraulics.
Slip rings in machinery for semiconductor processing
Within those machines, slip rings (as well as slip rings combined with rotary unions) often work on indexing platforms to process wafers mechanically and chemically …
… where manufacture can involve the application of materials and fluids.
Case in point: During the process of chemical mechanical planarization — a process that usually comes late in semiconductor processing, so must go quickly — integrated slip-ring rotary unions excel … especially with features to withstand the corrosive and abrasive setting.
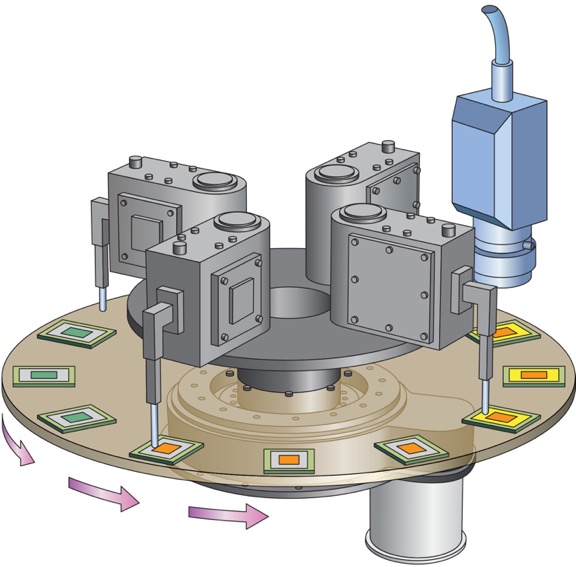
Indexing image courtesy Nexen Group • Watch the manufacturer’s Design World webinar on demand at designworldonline.com/how-to-build-rotary-indexing-tables.
Slip rings in aerospace, defense, and marine
In the aerospace industry, spacecraft solar arrays use small slip rings that mount at their rotor to panel-moving actuator outputs. In a similar application in defense, slip rings work in armored-vehicle turrets to allow elimination of separate turret or gunner-station batteries. Here, a major environmental challenge is maintaining reliable power, data, and even video-stream connectivity even in the face of vibration.
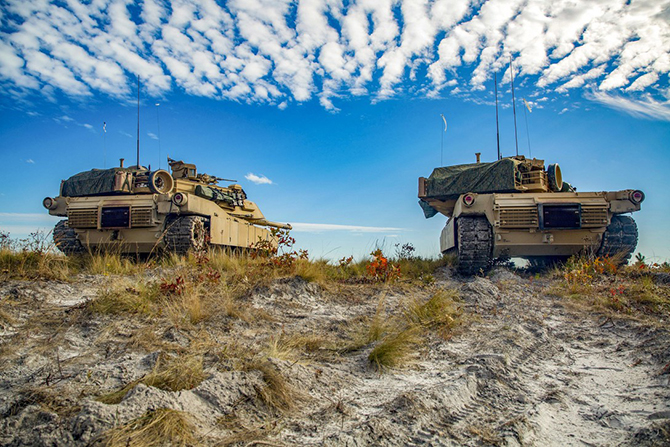
DoD photo: Marine Corps Cpl. Alexander Sturdivant • Marines provide security with M1A1 Abrams tanks during breaching operations as part of a field exercise at Camp Lejeune, N.C.
Slip rings complete marine designs such as cruise liners, icebreakers, Coast Guard vessels, and offshore platforms. One design making heavy use of slip rings is radar towers.
Slip rings also support the functions of remotely operated vehicles or ROVs and other designs for underwater. These are not unlike submerged applications where the slip ring is exposed to oil — as in the machine-tool industry, for example.
Recently Deublin worked on a slip ring that needed an IP67 rating for submergibility to one meter. The sealing effectiveness was paramount. The manufacturer ran a sealed slip ring underwater and passed the test. To be clear, high seal ratings such as IP67 are usually custom specified.

NASA photo | The International Space Station is seen from Space Shuttle Discovery. Solar arrays power the ISS and rely on specialty slip rings for power and data transmission in the challenging vacuum environment.
Slip rings in the packaging industry
Let’s consider SRC and SRD electrical slip rings from Deublin. These are specific to machines to support the packaging of pharmaceutical, food and beverage, and other consumable goods. These are setup to be modular and configurable — with up to 40 electrical channels and top speeds to 250 rpm … which is key in packaging that relies on speedy throughput for profitability.
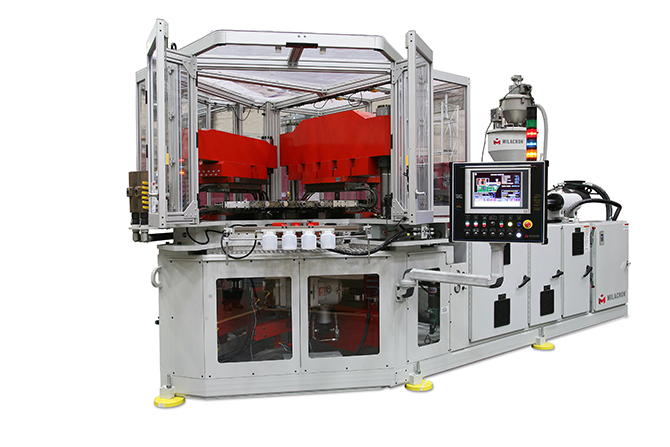
Uniloy injection-blow UIB 199 machine example courtesy Milacron
Some of the challenges are more specific: For example, machines involving plastics that need to be melted for molding or recycling might subject slip rings to ambient temperatures reaching 150° C.
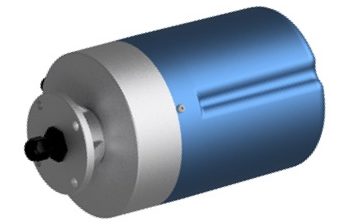
SRD electrical slip ring from Deublin
Of course, slip rings that transmit energy will generate their own heat — a pertinent design consideration when already operating in hot settings.
One last slip-ring application: Synchronous electric motors
Slip rings find use in the startup of asynchronous electric motors — in the ac induction motors known as wound-rotor motors. Here, they don’t transfer power. Rather, they insert resistance into rotor windings.To be clear — a slip ring in a motor is not the same as a commutator. Yes, their designs and functions are similar. But a ring in a slip ring is continuous. In contrast, commutators are segmented. Read more on this topic at the post: What is a wound rotor motor?
In short, slip rings in wound-rotor motors have three circuits. The rings are on the motor shaft (isolated) and made of copper or an alloy.
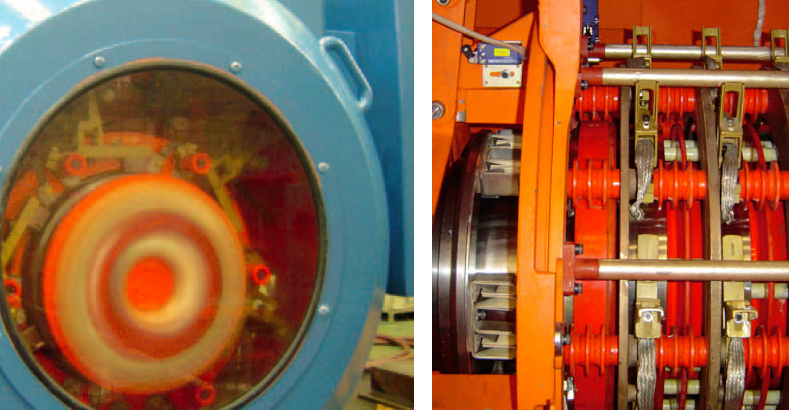
Photos: WEG Electric Corp.
Each connect to one of three rotor-winding phases. Graphite brushes connect to a rheostat or other resistive device. When the slip ring turns with the rotor, the brushes ride those rings and impart resistance to the rotor windings. That brings rotor current more in-phase with stator current. This boosts torque output with relatively low current. After the motor start-up sequence ends (and the motor reaches full speed) the slip rings short out and lose contact (to avoid dings to efficiency and torque they’d otherwise impart) and let that motor run as a standard ac induction motor.
Filed Under: Slip rings + rotary unions, Motion Control Tips
Tell Us What You Think!