Design engineers identify the need for a slip ring in the very first stages of the design process — as usually there are no viable alternative solutions.
Of course, while engineers know near the beginning of the design process whether they need a slip ring, the slip-ring design details are usually developed and finalized with the manufacturer.
The most common slip-ring assemblies use metal rings or traces on one subcomponent. Then these interface with graphite or wire brushes that ride the rings’ surfaces. So as that metal ring spins, transmissions conduct via the ring to the brush or vice versa.
Where the application needs multiple contacts — which is usually the case — more ring-brush pairs stack along the Z axis. In some cases, manufacturers make their designs more compact by stacking the brushes on two sides of the slip-ring assembly.
A webinar on this topic was presented live on Tuesday, December 18, 2018. Click below to watch it on demand.
Metal rings for signal transmission are sometimes plated with silver, rhodium, or gold; those for power transmission are sometimes brass or (for higher rpms) phosphor-bronze.
Slip rings that use fiber-optic technology
Fiber-optic slip rings are usually called fiber optic rotary joints or FORJs for short. Some manufacturers partner with suppliers to combine fiber-optic rotary joints with other technologies that are suitable for the transmission of high power … and recognize the technology’s place in complementing other slip-ring power and data transfer options.
Data signals transmit well over FORJs — with 100 Gbps a typical speed. Plus data transfer isn’t affected at all by EMI from high frequencies. FORJs also excel where data loss can arise from resistance — and on axes with exceptionally high rpm.

Remotely operated vehicle (ROV) example courtesy NOAA. Click the gif to watch the full video.
FORJs are not without challenges … in suboptimal or compromised installations exhibiting connector issues; signal degradation in the form of polarization, wavelength, return, and insertion-related losses; more challenging engineering for multiple channels (to avoid crosstalk and other issues); and the need for higher levels of protection should the slip ring operate in harsh settings. As always, the application will dictate which technology is most suitable.
Fiber-optic slip rings often allow multiplexing or muxing — the transmission of multiple signals or data streams at one trace and at once. That allows for the full use of the optical lines’ high speed. Systems combining signals often use time-division multiplexers, which gives each independent signal a time window at an output. Other systems often use what’s called wavelength-division multiplexing — which gives each independent signal on the line a set light wavelength for transmission. This in turn boosts line capacity, speed, and scalability.
Side note on slip rings incorporated into rotary unions
It’s common for OEMs to specify slip rings with rotary unions where a machine build needs both … as they serve similar purposes albeit with different media. Recall that a rotary union joins a stationary inlet with a rotating outlet and contains fluid under pressure or vacuum to maintain that fluid connection.
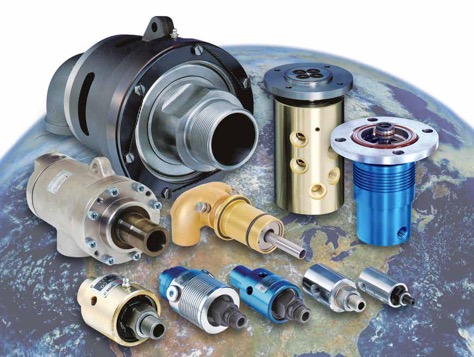
Deublin supplies rotary unions that incorporate slip rings.
Sometimes called swivel joints, these rotary unions integrate slip-ring subsystems quite well. One off-highway equipment example is a rotary union with integrated slip ring that transmits hydraulic fluid between an excavator’s track drive and its cab — even though the cab of the vehicle may turn 360° without limit.
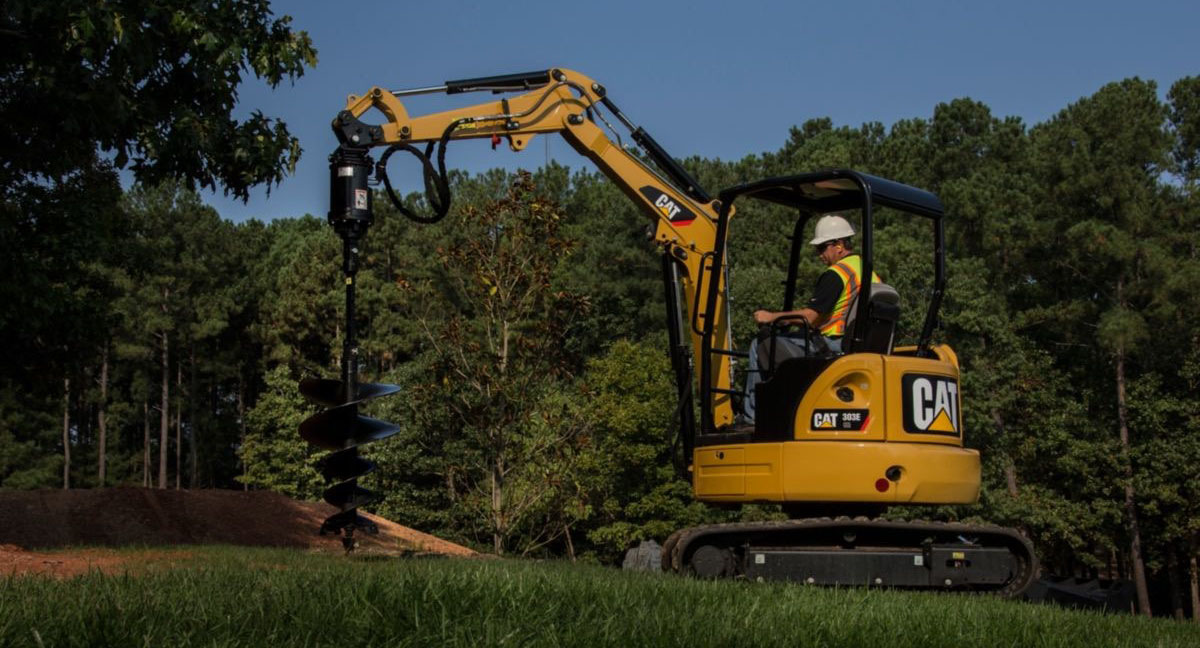
Rotary unions on off-highway equipment accommodate the transmission of signals and fluid power between cab and track base. Excavator image courtesy Caterpillar
Filed Under: Slip rings + rotary unions, Motion Control Tips
Tell Us What You Think!