Weatherproof gaskets protect equipment from harsh environmental conditions including heat, dirt, dust, rain, and snow. They are critical in such applications as renewable energy junction boxes, inverters, and other “connect-to-grid” enclosures, as well as others. Material and adhesive selection and testing are critical to the success of any weatherproof gasket application. Suitable materials for gaskets can include: silicone, neoprene, urethane, and ethylene propylene diene monomer (EPDM).
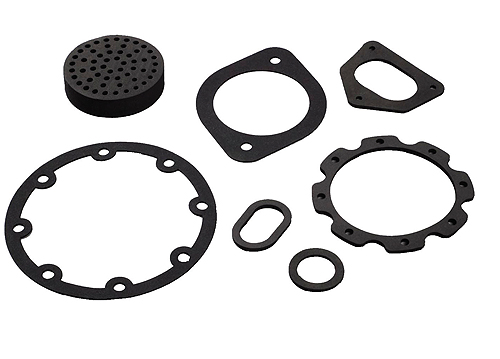
Understanding the environmental conditions where a gasket is to be used is critical to selecting the best material and gasket design for an application.
Silicone gaskets come as solid, sponge, or foam. Characteristics include resilience, high temperature stability, and general inertness. Solid silicone can be used with metal closures and requires good closure force. Silicon sponge has a closed cell structure suitable for environmental sealing applications. It can be used in both high- and low-temperature environments. Silicone sponge firmness is measured in psi. Two to 5 psi compression is considered soft, with 14 to 20 psi considered firm. Silicone foam with a closed cell structure is also suited for an environmental enclosure. It is stable under UV. Silicone provides a number of advantages:
• Waterproof – won’t break down over time with exposure to water
• Flexible – won’t freeze or crack at high or low temperatures
• Shrink-proof – won’t shrink over its lifetime
Neoprene is a synthetic rubber produced by the polymerization of chloroprene. The material has good resilience, tear strength, and resistance to UV and ozone damage. However, neoprene is easily damaged by petroleum-based fuels. Neoprene can withstand temperatures up to 250°F, and low temperatures to -40°F. Neoprene and foamed neoprene characteristics are:
• Good chemical stability – flexibility over a wide temperature range
• Waterproof and corrosion resistant
• Permanent seal – not meant to be broken and re-established
Urethanes can also be used for gasket materials in various blends and formulations. They provide good aging and abrasion characteristics, but are not suitable for very high temperatures. Urethane gaskets characteristics:
• Flexible – conform to the shape of the application
• Waterproof – withstand changing weather conditions
• Elastic – remains flexible despite temperature changes
EPDM is a closed cell sponge rubber material that exhibits good aging properties, compressibility, and resistance to ozone and oxidation. EPDM is available in a number of densities exhibiting varying degrees of hardness. EPDM weatherproof gaskets characteristics:
• Wide temperature range – withstand high temperatures, to 300°F and very low temperatures to -60°F
• Waterproof – withstand moisture
• Resistance to aging – withstands UV, ozone, and oxidation
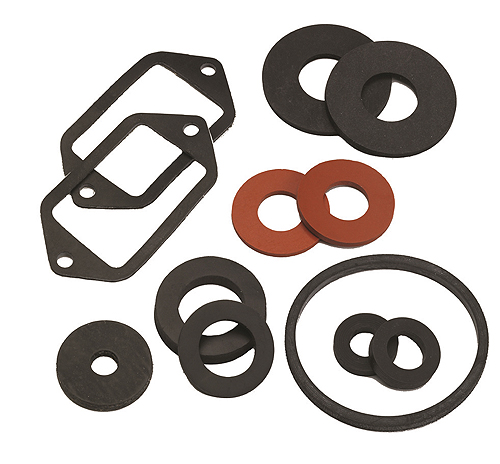
A synthetic rubber offers good chemical stability, water and corrosion resistant, and is a good permanent seal.
When working with a manufacturer for the gasket, check to see if they offer the following manufacturing capabilities:
• Precision die-cutting – which can be executed with a punch press, flatbed presses, servo-driven rotary die-cutting, CNC die-cutting, laser die-cutting, and a Zund die-less cutter.
• Slitting and rewinding – some manufacturers offer ranges from 0.1875-in. to 78-in. wide and 0.00048-in. to 0.093-in. thick. Razor, shear, bologna, lathe, and crush slitting are available.
• Water jet cutting – for materials from foams to durable sheet stocks. This machining capability suits parts with intricate profiles to avoid edge degradation.
• Ultrasonic welding – an alternative to adhesives for joining plastic to plastic and plastic to metal.
• Creasing/cuffing – automated processes for close-tolerance finishing.
Fabrico
www.fabrico.com
Filed Under: Seals • O rings, Materials • advanced, Seals
Is an EPDM flange gasket okay to use in a soft water system?
I NEED SOME GUIDANCE ON THE USE OF NEOPRENE OR SILICONE GASKET MATERIAL IN A PURGE PRESSURE SYSTEM IN A CLASS 1 DIV 2 ENVIRONMENT