Conveyors today are high-performance motion systems that incorporate more engineering than ever before. They outperform legacy iterations thanks to material advances and modular builds to suit specific applications. More specifically, many of today’s conveyors, from large conveyors for material handling to miniature varieties engineered for discrete product sorting, sport increasingly job-specific features.
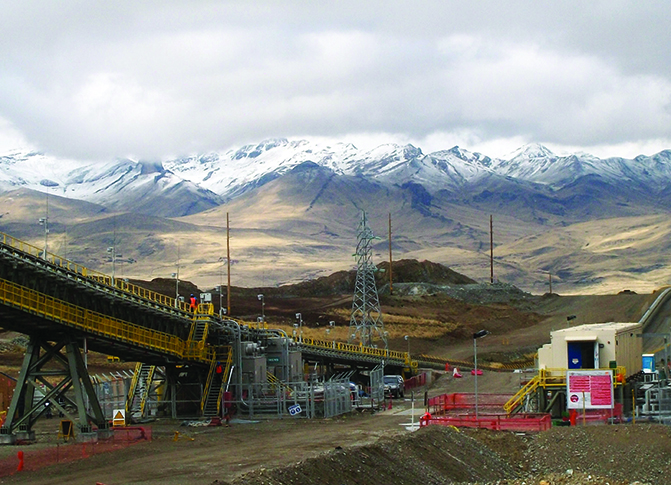
This 10-ft-by-4-ft 3200 Series in-feed conveyor precisely transfers and accumulates parts. It comes with V-guided belts for belt tracking and rack-and-pinion tensioning for easy belt changes and adjustments.
Just consider how many new facilities mostly rely on miniature conveyors to process pharmaceutical and medical products. Here, plant engineers are turning to conveyor specialists, even to get frames made. Such integrators and custom-conveyor manufacturers generally avoid the pitfalls of traditional conveyors—namely, overbuilt frames and oversized mechanical components such as bearings. Safety margins are tighter but more precisely matched to the application, which supports another trend in automation and manufacturing toward leaner operations. One caveat: Customizing job-appropriate conveyors can be a challenge where the manufacturer must account for complex parts handling and orientation.
Consider medical and product handling: Parts are often small and fragile, so are difficult to handle, orient and transfer between processing stations. In the past, most manufacturers shied away from designing conveyors for such applications, according to Mike Hosch, V.P. of the Industrial Products Group at Dorner Mfg. That’s because conveyors that move and handle tiny medical and pharmaceutical products need miniature bearings with long lives; small durable drives; short belts with consistent fabrication; and effective use of product space.

Some conveyor chain (as that shown here) makes efficient in-line self-clearing nose-over transfers. This is Rexnord 1553 Low Backline Pressure (LBP) MatTop chain for food and beverage, liquid, and warehouse and distribution applications.
“Some such miniature conveyors have end rollers of just more than half an inch, so they fit into tight machine spaces and transfer products less than an inch in diameter when run end-to-end,” said Hosch. Here, the conveyor frame fully encapsulates bearing housings, so end users can also put the conveyors side by side and get them nearly flush with only a 1⁄4-in. gap from belt edge to belt edge.

InnerDrive Belt Conveyors from QC Industries house an efficient 24-vdc motor within their frames, so they need less space than traditional conveyor drive packages. Frame height is 2.54 in., so this conveyor fits into tight spaces where others don’t.
Consider just one example: Many low-profile conveyors benefit from specialty actuation, and the trend is toward pinch drives. Typical belt conveyors run under tension to give the drive roller traction to run the belt, but that necessitates oversized bearings and rollers. In contrast, pinch drives let conveyors run with almost no belt tension, explained Hosch. A conveyor uses two pinch-drive mechanisms, each spring loaded against the drive roller—so the belt can run in either direction under just enough tension to keep the belt flat. Pinch drives force the conveyor belt against the drive roller to give it driving traction without tension. Without the need for high tension, the belt lays flatter, which helps keep lightweight components upright.

This unusual conveyor design from iwis drive systems, LLC conveys beverage cans around production processes. Called the POChain-I, it’s part of a larger industry trend towards cost-effective options that are explicitly tailored to specific applications.
“Medical, pharmaceutical and assembling industries have always needed miniature conveyors, but didn’t have many options. That’s changing now,” said Hosch.
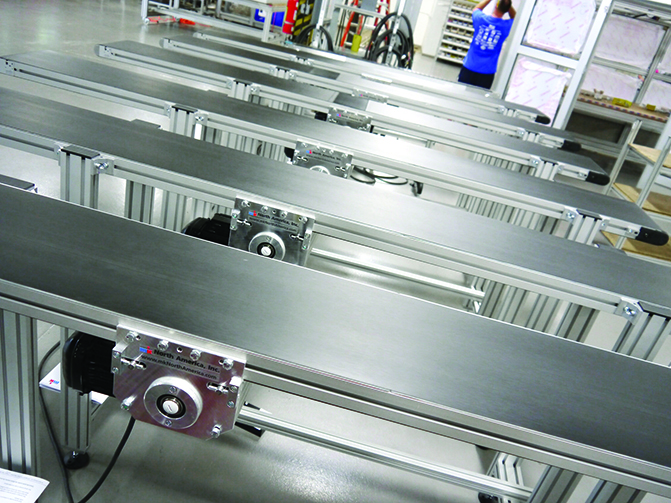
mk North America offers more than 20 different conveying systems for long life and reliable operation, including these flat belt conveyors.
Filed Under: Linear Motion Tips