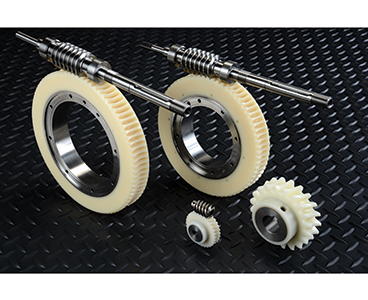
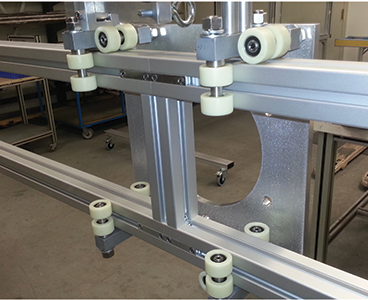
INTECH Power-Core™ components require no lubrication. They are corrosion resistant, do not swell in moisture, absorb shock and vibration, and reduce wear, noise, and inertia vs. conventional metal or plastic components.
In addition, INTECH Power-Core components put an end to metal-to-metal wear on steel or aluminum. So, no more metal particle contamination occurs. The need to caseharden and grind contact surfaces is eliminated. And no central lubrication system is required.
Today INTECH is a leader in the engineering and design of precision-machined Power-Core gears, guide rollers, and cam followers.
The expected life of INTECH’s innovative gears with integral metal core can be calculated. The outer plastic layer of the gear is attached to an inner metal core in an inseparable bond, even at high temperatures. The metal hub ensures higher torque transmission and secure attachment to the shaft. The core also helps reduce thermal expansion in the plastic outer portion of the gear by up to 50%. Reduced thermal expansion and dimensional stability in moisture allow machining of high AGMA, 10+, class gears. The inner core is available in carbon or stainless steel. And also in aluminum for corrosive or low-inertia applications.
Physical properties of INTECH Power-Core™ enable our components to satisfy demands for higher machine speeds, greater reliability, and lower maintenance. Intech engineers analyze stress and other key factors to accurately predict expected useful gear life and durability in your applications.
To date, more than 25,000 Intech PowerCore gears have been sold worldwide for use in a wide range of applications. These include medical equipment, packaging, food processing, clean room automation, paper converting, aerospace, architectural, robotics, manufacturing, and many others.